What Is ALD Coating?
Atomic Layer Deposition (ALD) is a controlled form of chemical vapor deposition (CVD). ALD uses timed pulses of reactive precursors to encapsulate all exposed surfaces of a substrate for coating. It gets its name from the nature of these pulses, each of which deposits a single self-terminating layer.
By alternating the chemicals present in the chamber, the chemistry and thickness of the coating can be controlled with atomic precision. Because ALD uses gas-phase chemistry to make coatings, it is able to deposit coatings on all surfaces which the gas can reach providing the opportunity to precisely coat parts even with extremely complex shapes.
COATING OPTIONS WITH ALD
Atomic Layer Deposition affords a wide range of coating compositions. It is commonly used to manufacture encapsulating coatings of insulators to exclude liquids or gasses from sensitive components. ALD uses no plasmas making it ideal for a variety of delicate substrates. Commonly made coatings via ALD include:
- Silicon Oxide
- Aluminum Oxide
- Titanium Nitride
- Lithium Fluoride
Common Applications of ALD Coating
Atomic layer deposition is best utilized in applications requiring precise thickness control and conformal coating where line of sight deposition is not possible.
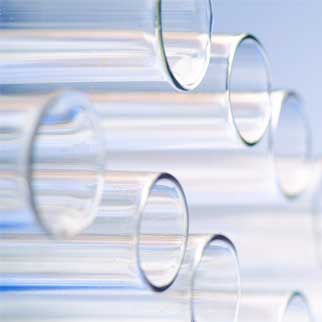
Apply an etch resistant coating to the interior and exterior surfaces of quartz tubes used in inductive plasma generators.
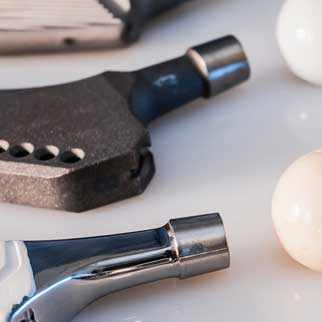
Titanium oxide encapsulation of surgical devices and implants.
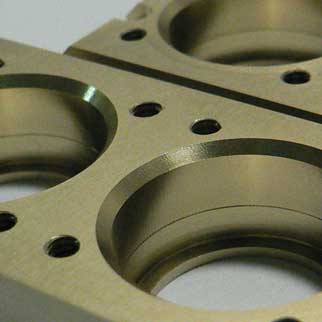