Alcadyne’s primary coating process is physical vapor deposition (“PVD”) or PVD coating, a technique that describes a variety of vacuum deposition methods, such as cathodic arc, sputtering, and evaporation.
PVD coatings are thin film coatings where a solid material is vaporized in a vacuum chamber and deposited onto a target material. It is used to change the surface properties of the object to be coated, where new mechanical, chemical, electrical or optical characteristics are needed.
PVD coatings result in extreme surface hardness, low coefficient of friction, anti-corrosion, and wear resistance properties.
The Process
The process is carried out in a vacuum chamber at a temperature between 50 and 600 degrees Celsius and is known as a “line of sight” technique, meaning that the atoms that are vaporized from the solid material travel through the vacuum chamber and embed themselves into whatever object is in its path. Therefore, in order to coat the proper location of the object we must position the object in the chamber appropriately or rotate the object during deposition to completely coat the part.
Different types of PVD coatings will result in different material properties. Even though a coating may look the same or is made from the same material, how you make the coating has a strong impact on the properties of the coating and how it will perform in the application required.
These are thin film coatings – typically anywhere from 0.5 microns to 5 microns – that won’t throw an engineered part out of spec
The Coating Materials
Common PVD coating materials are titanium, zirconium, aluminum, stainless steel and copper, though gold for aerospace electronics is often requested. And these coatings can be applied to a wide variety of substrates, including nylon, plastics, glass, ceramics and metals, such as stainless steel and aluminum.
The Applications
There is a wide range of applications for PVD, which is why it is commonly used in high-tech industries. Some of the industries and applications in which we have applied PVD coatings include coating on composites for aerospace, titanium on medical implants and surgical tools, gold thin film to replace plating for electronics, non-metal, chemical resistant oxides for semiconductor parts and hard ceramic coatings for industrial tools.
If you have a need to change the surface properties of a part to achieve an enhanced material, please give us a call to discuss with our technical team.
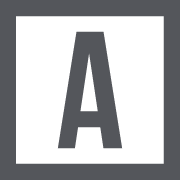