We’re always testing the boundaries of what’s possible with surface modification. From Injection Molds to semiconductors, we coat products subjected to a range of harsh conditions. One area that presents a wealth of opportunity—where we’re extensively testing and a little bit obsessed—is 3D printing.
Surface modification is proving to be a game-changer for products in need of wear resistance. But before we get ahead of ourselves, let’s look at a recent project we completed with Formlabs to see why we’re so excited.
Formlabs sent us a pump housing printed with Tough 2000 resin using a Formlabs Form 3 SLA printer. We took the Formlabs pump housing and applied a Titanium Nitride coating. Our PVD coating process is capable of reaching deep channels and coating odd geometries, so the rounded bell chamber of the pump housing was completely conformally coated. A 5 micron thick layer of Titanium Nitride was applied to the pump.
Take a look at the before and after shots to see the change for yourself.
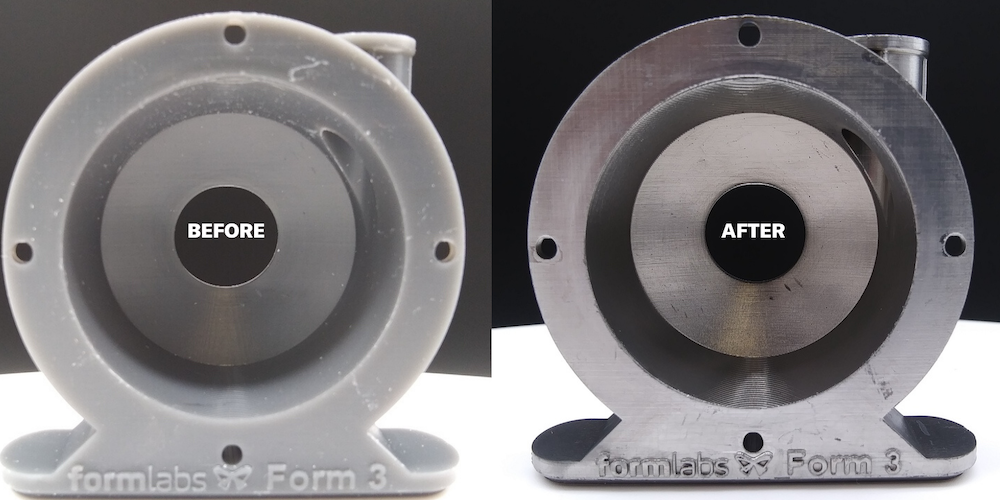
This Formlabs project is a nice visual example of leveraging surface modification to transform 3D parts. However, let’s take a deeper look at the benefits of coating a 3D printed part that you can’t necessarily see in a photo. These include:
- Chemical Resistance
- Abrasion Resistance
- Shielding, conductivity, or grounding
- Release coating
- Bridging layer for incompatible materials
And for good measure, let’s look at a few other additive manufacturing cases to see how we’re using surface modification to solve problems in the additive manufacturing industry.
In one application, a nylon 3D printed part had a short lifespan due to the polishing slurry the semiconductor manufacturer uses for cleaning their chambers. We coated the part with stainless steel to protect the nylon from the polishing slurry.
A similar application for a nylon 3D printed bushing used in the oilfield was failing because of oil absorption in the part as well as wear and tear. We coated the part with stainless steel to improve wear resistance and increase the life expectancy of the bushing.
We have been coating PEEK (polyetheretherketone – say that ten times fast) spinal implants with Titanium to promote bone attachment, as PEEK-only implants are encapsulated which translates into serious issues for patients.
Long story short, additive manufactured, or 3D printed, parts can benefit from surface coatings just like traditional CNC and molded parts.
If you want to dig in and chat about problems you’re trying to solve, let’s chat.